Not known Details About Alcast Company
Table of ContentsAlcast Company for DummiesAll About Alcast CompanyThe Greatest Guide To Alcast CompanyRumored Buzz on Alcast CompanySome Ideas on Alcast Company You Should KnowThe 9-Minute Rule for Alcast Company
Chemical Contrast of Cast Light weight aluminum Alloys Silicon advertises castability by lowering the alloy's melting temperature level and boosting fluidness throughout spreading. In addition, silicon adds to the alloy's toughness and use resistance, making it useful in applications where longevity is crucial, such as automobile parts and engine elements.It likewise improves the machinability of the alloy, making it simpler to process into finished products. By doing this, iron adds to the overall workability of light weight aluminum alloys. Copper raises electric conductivity, making it helpful in electrical applications. It also enhances rust resistance and includes in the alloy's overall stamina.
Manganese adds to the strength of aluminum alloys and boosts workability (Foundry). It is typically used in functioned light weight aluminum items like sheets, extrusions, and accounts. The visibility of manganese help in the alloy's formability and resistance to splitting during construction procedures. Magnesium is a light-weight element that provides toughness and influence resistance to aluminum alloys.
Alcast Company Fundamentals Explained
It permits the production of lightweight components with excellent mechanical buildings. Zinc improves the castability of aluminum alloys and assists control the solidification process throughout casting. It improves the alloy's toughness and hardness. It is commonly discovered in applications where complex forms and fine details are necessary, such as decorative spreadings and certain vehicle parts.

The primary thermal conductivity, tensile toughness, return strength, and prolongation differ. Select ideal basic materials according to the performance of the target product created. Among the above alloys, A356 has the highest thermal conductivity, and A380 and ADC12 have the least expensive. The tensile limit is the contrary. A360 has the finest yield strength and the highest elongation price.
Alcast Company for Beginners
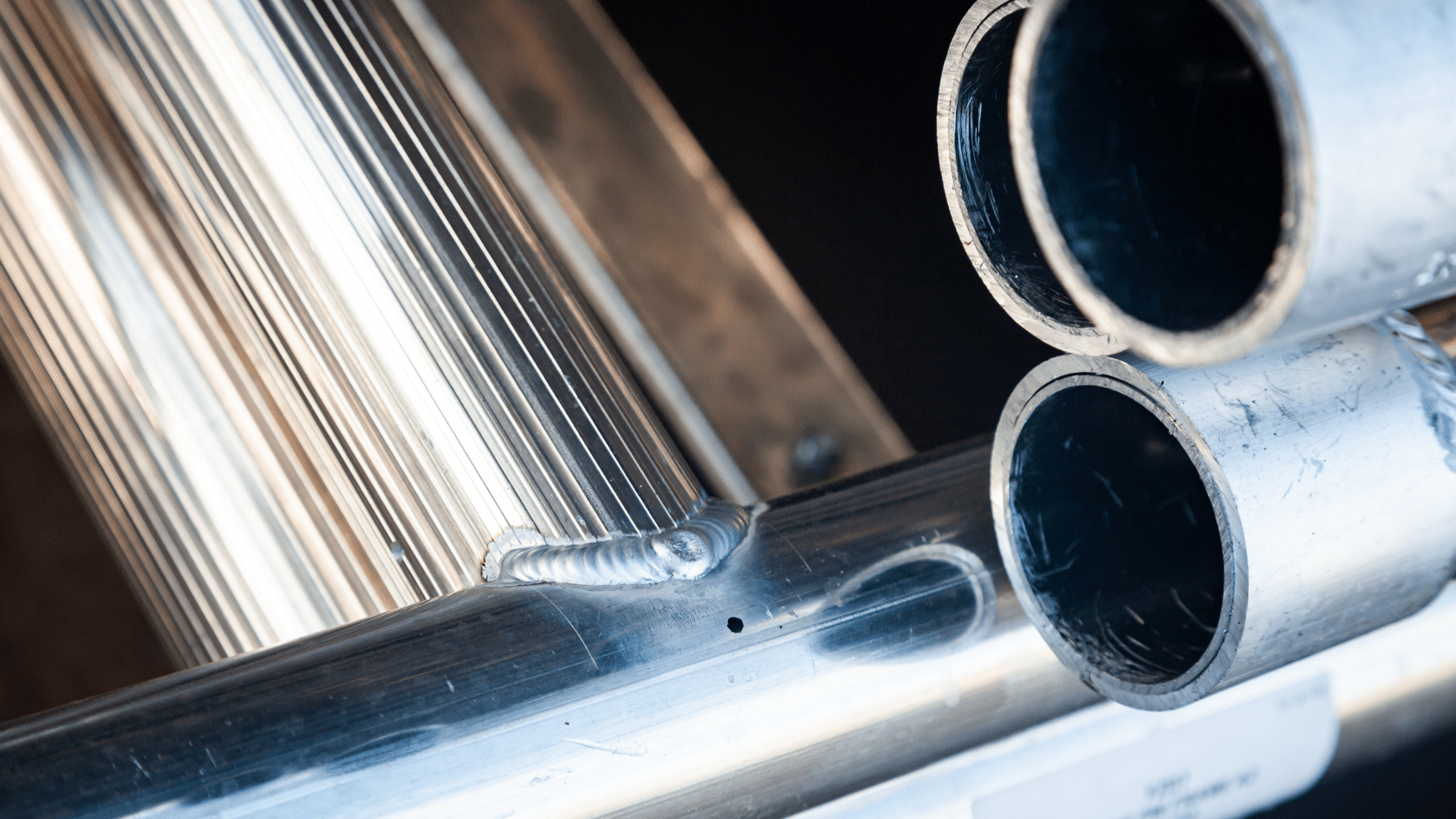
In precision great site spreading, 6063 is appropriate for applications where intricate geometries and top quality surface area coatings are critical. Examples consist of telecommunication rooms, where the alloy's remarkable formability permits streamlined and cosmetically pleasing designs while preserving structural honesty. Likewise, in the Illumination Solutions industry, precision-cast 6063 parts create sophisticated and efficient lights fixtures that call for elaborate shapes and good thermal performance.
It results in a better surface area coating and better deterioration resistance in A360. The A360 displays remarkable elongation, making it excellent for complex and thin-walled parts. In precision casting applications, A360 is appropriate for sectors such as Consumer Electronics, Telecommunication, and Power Tools. Its enhanced fluidness enables for intricate, high-precision components like smartphone cases and communication device real estates.
Alcast Company Can Be Fun For Everyone
Its unique homes make A360 a valuable choice for accuracy casting in these industries, improving product durability and quality. Aluminum alloy 380, or A380, is an extensively utilized casting alloy with a number of distinct attributes. It supplies exceptional castability, making it an optimal choice for precision spreading. A380 shows good fluidness when molten, ensuring detailed and in-depth mold and mildews are properly recreated.
In precision spreading, light weight aluminum 413 shines in the Customer Electronic Devices and Power Devices industries. This alloy's remarkable corrosion resistance makes it an outstanding selection for outside applications, guaranteeing lasting, long lasting items in the discussed sectors.
Rumored Buzz on Alcast Company
Once you have chosen that the light weight aluminum die casting procedure is ideal for your project, a crucial next action is choosing one of the most proper alloy. The aluminum alloy you pick will considerably influence both the casting process and the buildings of the end product. Due to this, you need to make your decision carefully and take an educated strategy.
Identifying the most appropriate light weight aluminum alloy for your application will certainly indicate weighing a vast selection of features. These relative alloy qualities adhere to the North American Die Spreading Association's standards, and we have actually divided them right into 2 groups. The initial classification addresses alloy qualities that influence the manufacturing procedure. The second covers attributes influencing the buildings of the end product.
Little Known Questions About Alcast Company.
The alloy you choose for die spreading straight impacts several elements of the spreading procedure, like exactly how easy the alloy is to work with and if it is prone to casting defects. Hot splitting, likewise called solidification splitting, is a common die spreading flaw for light weight aluminum alloys that can cause interior or surface-level rips or fractures.
Specific light weight aluminum alloys are a lot more susceptible to warm cracking than others, and your selection must consider this. Another common issue located in the die casting of light weight aluminum is pass away soldering, which is when the actors adheres to the die wall surfaces and makes ejection tough. It can damage both the cast and the die, so you should look for alloys with high anti-soldering properties.
Rust resistance, which is already a notable feature of aluminum, can differ significantly from alloy to alloy and is an essential characteristic to think about depending upon the environmental conditions your product will be revealed to (Aluminum Castings). Put on resistance is an additional property typically sought in light weight aluminum products and can differentiate some alloys